404 Error
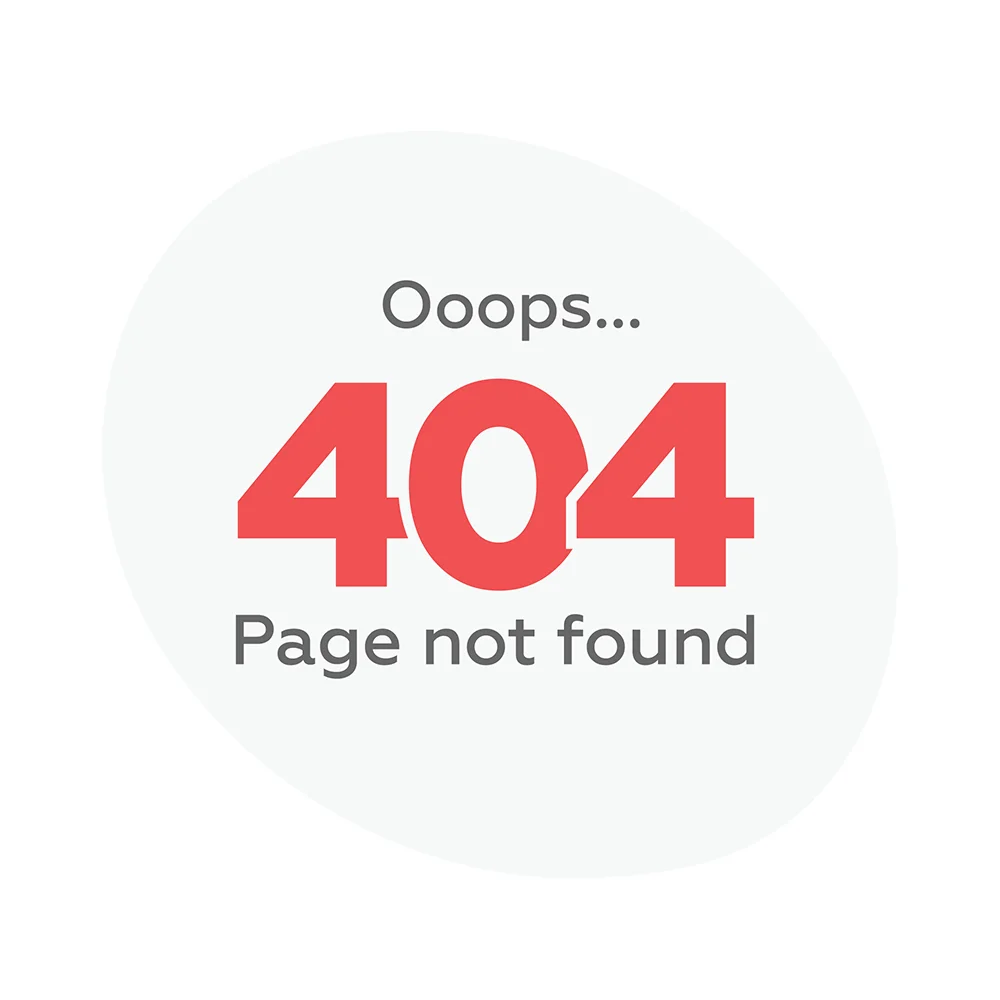
The page you are looking for cannot be found. Please try using the site search located at the top to find your page.
You can also browse our capability pages to find examples of our work and other relevant information.
- Research & University Partnerships
- Epidemiology & Exposure Science
- Radiation Safety & Health Physics Training
- Evaluation Support
- K-12 STEM Programs
- Public Health & Healthcare
- Workforce Solutions
- Peer Review & Grants Management
- Environmental Services
- Forensic Science Services
- Technology Products & Solutions
If you are interested in learning about health physics artifacts, visit the ORAU Museum of Radiation and Radioactivity.